So what is 100% OEE and how is it calculated? Full resource efficiency (100%) means that all staffed time is used to produce (only) top-quality products at (only) full technical speed.
Overall equipment effectiveness (OEE) is a term used to evaluate how effectively a manufacturing operation is utilized. The term was coined by Seiichi Nakajima in the 1960s.
You can immediately discount the possibility of 100% OEE being something you can maintain over longer periods. In certain industries, it is possible to be very near to 100% over e.g. one shift, but sooner or later maintenance/servicing will be needed and very often article changeover as well.
The basic mathematical formula for OEE is very straightforward:
OEE = Produced approved amount / technical maximum amount
60 approved items in an 8-hour shift, where 10 can be produced in one hour at full speed, results in an OEE of 75% (60 / (10x8) = 60 / 80 = 0.75).
But in order to describe how you get from this type of simpler statement to really being able to use the OEE-value in your production control, you need to look at the matter in a little greater detail. The OEE-value can also be calculated using three parameters multiplied together to give a product.
A | Machine availability | The proportion of planned time used for production |
P | Performance | The measured cycle time in comparison to the technical optimum cycle time |
Q | Quality outcome | The proportion of approved products |
OEE | Resource efficiency | A x P x Q |
What then is 100% Machine Availability? And what is 100% Performance? Now the question is getting a little more tricky.
The text books say that 100% machine availability is the total time devoted to an available order. In other words, when there is production to be done. A stop for e.g. maintenance must therefore be seen as a loss.
When it comes to 100% performance, things are a bit trickier still. The text books say that you have to bear in mind the technical maximum speed for which the plant (the machine) has been specified, designed and purchased. We will leave that for the moment and will come back to it later in the section dealing with the introduction of OEE-measurements in practice.
100% quality outcome is the most straightforward of the three. It is the percentage of a produced amount that can continue on to a customer (the next stage in the flow).
A frequent question is how to deal with rework. If you bear in mind that the same item needs to be dealt with twice, but that you have only produced one item, then you can see why it has to be dealt with as a speed loss in calculating the OEE-value.
All three parameters are expressed as percentages. This is because they relate to a definition of 100% that has to apply to any combination of machine/flow and article.
Because OEE is expressed as a percentage, it is also a relative value. This means that it describes resource efficiency relative to what you yourself have defined as 100%.
The upshot of this is that it is relatively easy to manipulate your OEE-value. In practice, this is one of the reasons why you should not compare OEE-values from different plants.
On the basis of the above statements, you can see that you are more or less forced into having an internal policy document that defines how OEE is to be calculated.
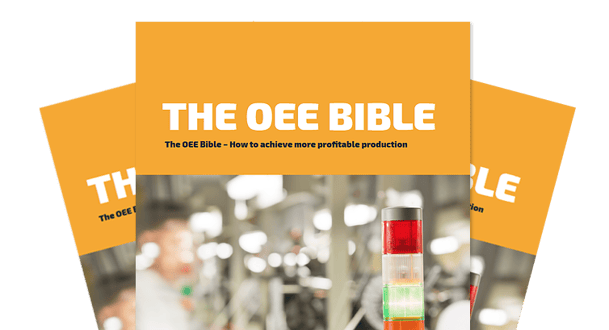